The various forms of expanded perlite—classic expanded particles, microspheres, and crushed flakes forms—deliver a variety of textured looks for a variety of applications.
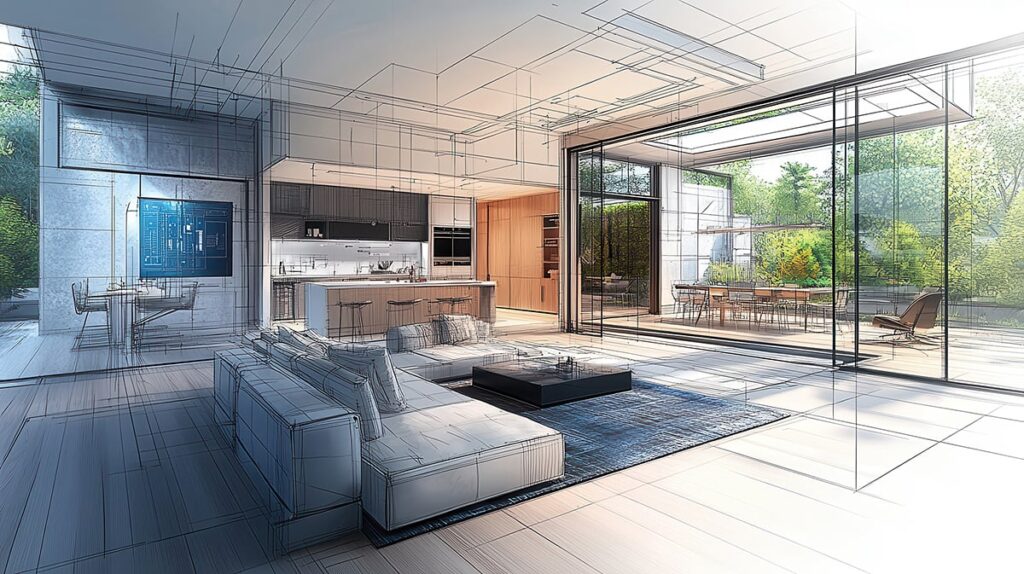
Perlite, a naturally occurring volcanic glass, has garnered significant attention as a versatile and sustainable material in various industrial applications. In the context of fillers, perlite enhances product properties, improves cost-efficiency, and contributes to the sustainability of composite materials. This article explores the diverse applications and benefits of perlite fillers, particularly focusing on classical expanded particles, microspheres, and crushed flakes forms.
Perlite for Textured Coatings and Paints Texturing
WHAT IS PERLITE?
Perlite is a naturally occurring silicious volcanic rock which presents the unique property of expansion four to twenty times its original volume when heated to a sufficient point in its softening range. This is because perlite contains 2 to 5 wt. % of different forms of water and, upon expansion and matrix melting, it vaporizes, subsequently forming a dense network of tiny bubbles along the glassy particles. These small bubbles trapped in glass are what give expanded perlite its remarkable physical characteristics.
One of the most distinctive features of expanded perlite that is created by the thermal treatment is its white color. Indeed, expanded perlite color ranges from snowy white to grayish white, depending on the quantity and type of impurities, while crude perlite color is translucent, light gray, or glossy black.
The bulk density of expanded perlite ranges between 30 and 240 kg/m3 depending on the expansion conditions, rendering it useful to various applications in the construction, industrial, chemical, horticultural and petrochemical industries. The unique properties of expanded perlite make it particularly useful in the manufacture of various oil and water-based textured coatings.
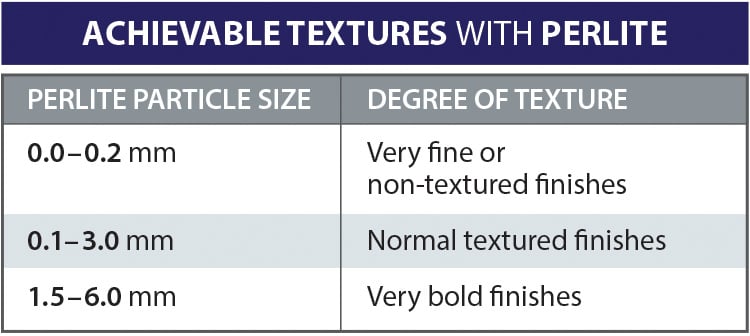
ADVANTAGES OF PERLITE
Perlite offers many benefits as fillers for both applicators and manufacturers, since it offers inexpensive bulk filling with minimal oil absorption. Combined with its pristine white finishing, it drastically reduces the pigment cost.
Additionally, due to the light weight of perlite, the textured coating does not tend to sag and run. The applicator can then apply thicker coats in a single pass, saving labor cost and reducing material losses. Perlite also does not induce yellowing in industrial environments because it is inorganic and inert. Even when perlite is used in coatings, it provides insulating properties to the final product due to its low thermal conductivity. In addition, the properties of expanded perlite have an anti-condensation effect on the finished surface.
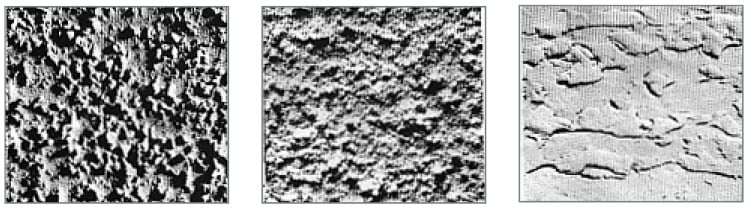
TEXTURE PAINTS
Texture paint is used as a cost-effective solution for hiding surface imperfections and flaws at the joints between drywall panels. Expanded perlite replaces sand and other compact fillers because it is as effective and less prone to settling into the paint.
The texture is dependent on the size of the filler. As a reference, the table below shows the textures that can be achieved using expanded perlite of different sizes. The data are approximate and are provided for guidance only.
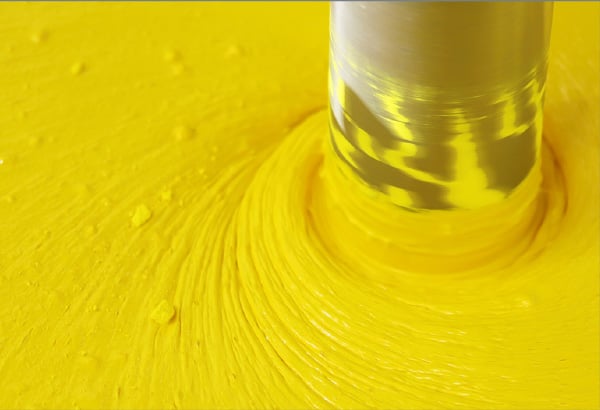
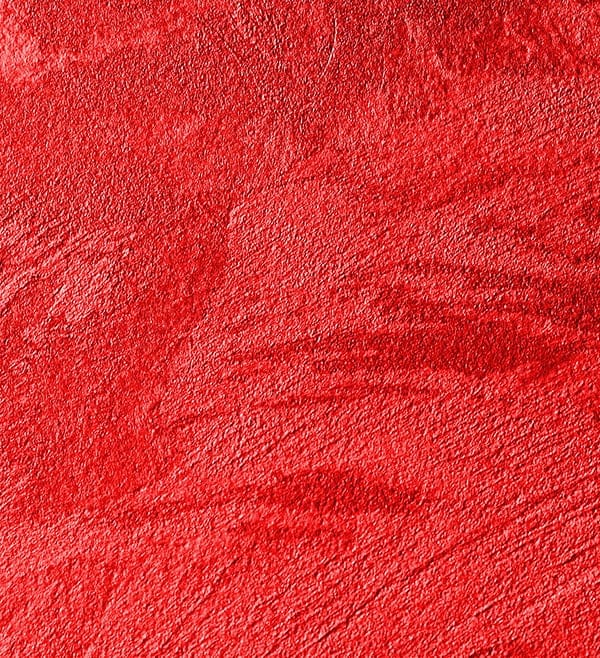
Perlite Volcanic Glass as Glass Flake Filler
Perlite glass flake is produced by further processing expanded perlite towards its crushing, a process that is also mandated for the production of filter aid materials. The large, rounded particles are milled to form glass flakes with an interlocking three-dimensional structure. This structure helps reduce shrinkage upon drying or curing, maintaining the physical dimension of a finished part. Applications in which perlite glass flakes are desired include their use as filler in water-based construction compounds, paints, asphalt, concrete, plaster, and resin-based castings. They are commonly used in elastomer formulations and specialty applications such as seed coatings as well. These flakes are generally smaller than 300 μm in diameter and, depending on the grade, average between 20 and 70 μm in diameter.
Perlite glass flakes are used to provide the following in a formulation:
- Weight reduction
- Shrink and/or crack resistance
- Whiteness
- Inertness and non-toxicity
- Low volume-based cost compared to binders and other fillers
- Water and/or air permeability
- Anti-condensation effect
- Impact resistance
- Machinability and ease of sanding
- Nail and screw hold ability
- Flexural strength modification
- Very fine texture in coatings
- Elimination of gloss and sheen
- Pigment extension (aluminum in asphalt roof coatings, for example)
- Improvement of physical properties at cryogenic temperatures
- Solid carrier for a liquid ingredient resulting in a more even dispersion in blends
Expanded Perlite Microspheres
Expanded perlite microspheres are lightweight, inert, and have excellent thermal and acoustic insulation properties. When used as fillers in coatings and paints, they provide several benefits including:
Improved Insulation: They enhance the thermal and acoustic insulation properties of the coatings.
Reduced Weight: Due to their lightweight nature, they help in reducing the overall weight of the
coatings and paints.
Enhanced Durability: They contribute to the durability and longevity of the coatings by improving
resistance to cracking and abrasion.
Cost-Effectiveness: They can be a cost-effective filler option due to their low density and high volume.
Reduced VOCs: They help in reducing the volatile organic compounds (VOCs) in paints, making them more environmentally friendly.
Expanded perlite microspheres are particularly useful in applications where these properties are desirable, such as in construction materials, industrial coatings, and specialty paints.
The Importance of Choosing the Right Mixing Procedure
Selecting the right mixing procedure for paints containing expanded perlite fillers, like microspheres, involves balancing the need for thorough mixing to reach the desirable homogeneity together with the necessity to protect the integrity of the fillers. It is thus needed to consider certain crucial factors such as rheology, shear rate, speed, and equipment compatibility to achieve a high-quality and uniform dispersion of fillers in the paint. The following needs to be considered in that case:
Shear Rate and Mixer Type: Expanded perlite particles are lightweight and can be fragile. Excessive shear can break down the microspheres, reducing their effectiveness. Choose mixers that provide sufficient mixing without applying excessive shear, such as paddle mixers or low-shear planetary mixers.
Durability of the Filler: As a rule of thumb, the higher the filler density, the greater the crush strength. Hence, if a particular grade is selected for its very low density, the manufacturing process must accommodate the filler’s inherent fragility.
Mixing Time: Trials must be done to determine optimal mixing time, which ensures homogeneity without fillers disintegration. Moreover, excessive mixing time can cause damage to the fillers or alter the paint properties.
Mixing Speed: Start with a lower mixing speed to incorporate the filler and gradually increase if needed. High initial speeds can cause the lightweight microspheres to fly out of the mixture.
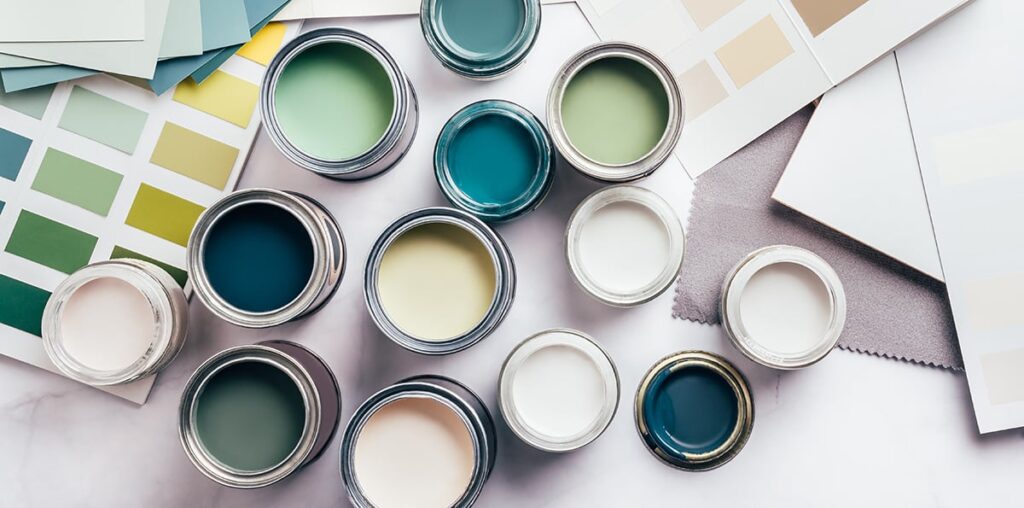
To download a .pdf of the Perlite as Filler in its Various Forms brochure, click here.
If you have technical questions on this topic, please email the technical contacts listed on our contact page.
Copyright © 2024 Perlite Institute All Rights Reserved