Perlite molded insulating products offer excellent thermal insulation properties that are lightweight, easy to install, customizable, and resistant to fire, moisture, and chemicals.
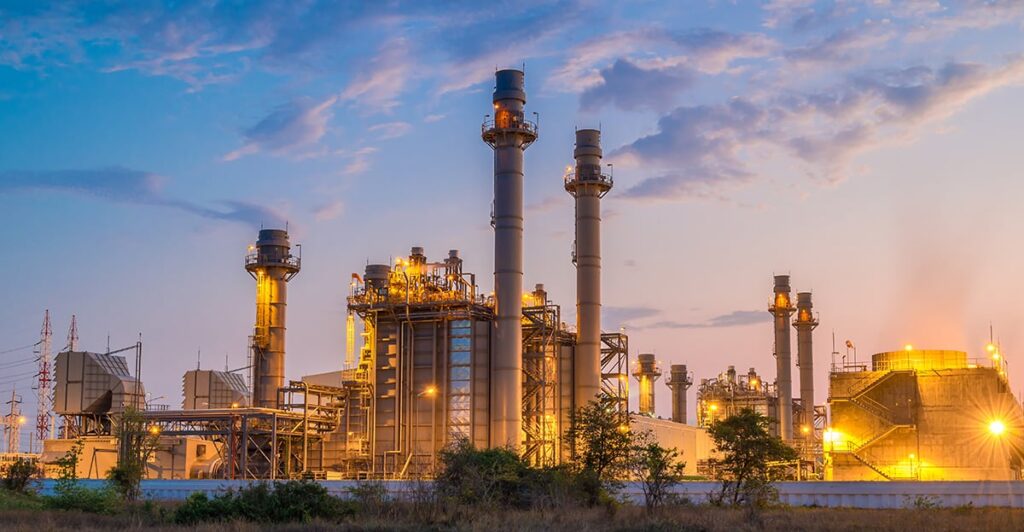
Perlite Molded Insulating Pipe and Block products are a type of thermal insulating material designed to provide superior insulation in a range of industrial applications. Made from expanded perlite—a form of naturally occurring volcanic glass that has been expanded with heat—perlite-molded products comply with ASTM C610, which sets out the specifications for these types of perlite thermal insulation products. This publication provides an overview of these products, including physical and thermal properties, applications, and installation considerations.
BENEFITS & ADVANTAGES:
- Low thermal conductivity
- Corrosion protection
- Retains strength at high temperatures
- Reduce energy & maintenance costs
- Moisture resistant
- Fire resistant
- Low shrinkage
- Asbestos free
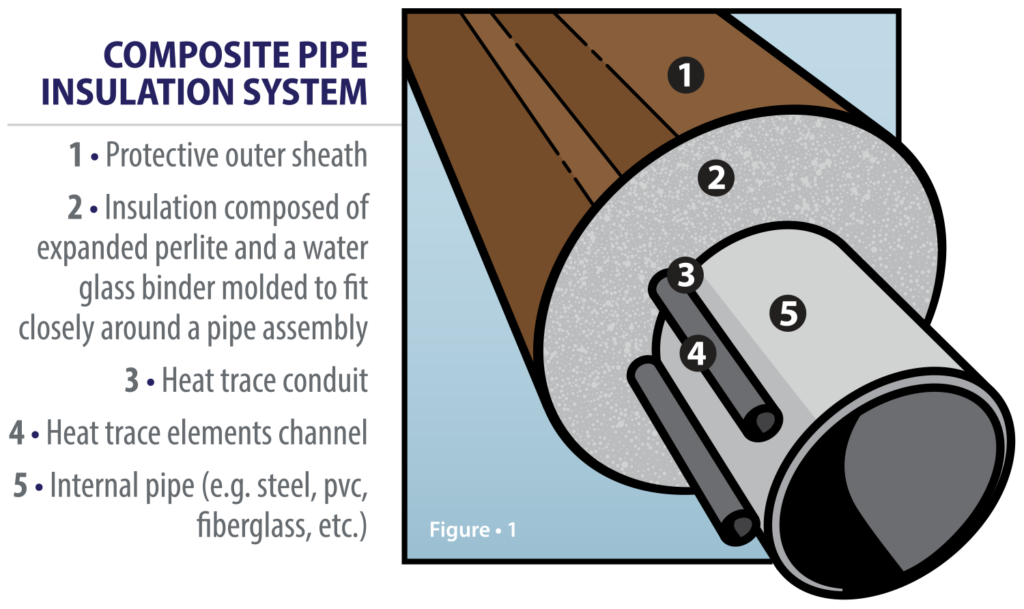
Product Characteristics
Perlite pipes and blocks are made from expanded perlite, which is produced by heating the raw perlite material to temperatures of around 850°C. Perlite is a naturally occurring, siliceous volcanic mineral that expands when heated to form tiny glass bubbles of entrapped air. The heating process causes moisture combined in the rock to escape in the form of steam causing tiny glass-like bubbles to form, resulting in a highly insulating material. The resultant ultra-lightweight material, referred to simply as expanded perlite, is durable, non-combustible (Class A1 / DIN 4102), inorganic, and ultra-lightweight with a bulk density range of between 40 kg/m³ and 190 kg/m³ (2.5 – 5 lb/ft³). It has an extremely low thermal conductivity at 0.044 W/mK (0.023 BTU/hr·ft·°F) in ambient conditions, and it is resistant to chemical attack, odorless and pH neutral.
Perlite pipes and blocks are produced using expanded perlite as their main constituent and are available in a range of sizes and thicknesses to suit different applications. Typical shapes are shown in Figure 2 and Figure 3.
The physical character of expanded perlite lends itself to a variety of special purposes, including its use as a functional filler material. Liquid sodium silicates (water glass) are used as binders to produce many formed products, such as ceiling tiles, pipe insulation, roofing boards and fire-rated door cores.
Molded perlite pipe and block insulation is defined by ASTM standards as insulation composed principally of expanded perlite, silicate binders and reinforcing fibers. As provided in ASTM C-610, perlite pipe and block insulation is rated for applications with operating temperatures up to 649 °C (1200 °F).
Perlite molded products are delivered in specialized packaging, to ensure a snug fit and to minimize breakage in transport. Once on-site, they can easily be cut to size or heat tracing elements installed, or incorporated as part of a composite system, such as the one shown in Figure 1.
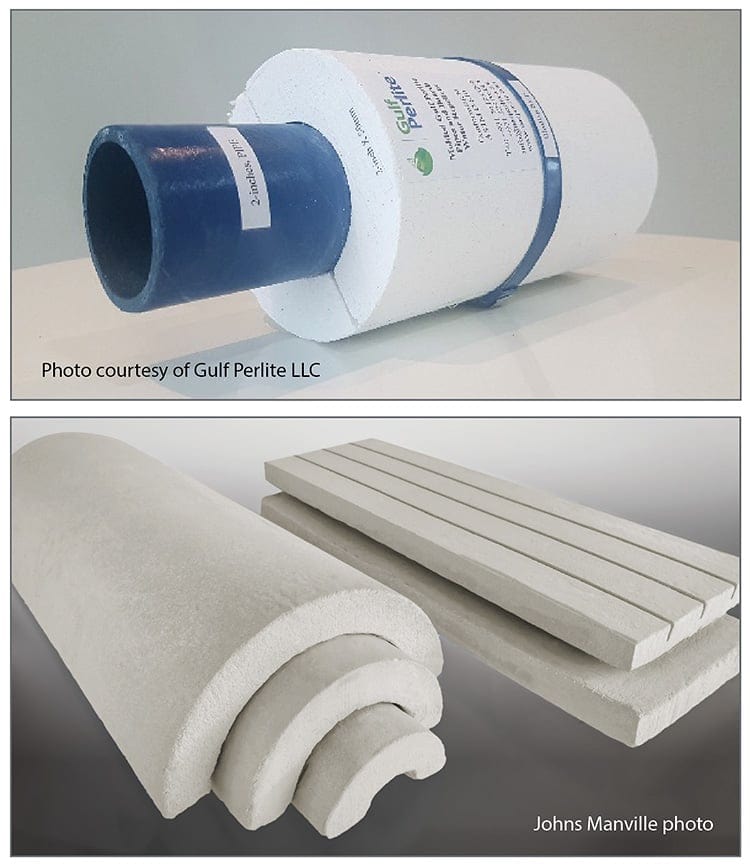
Figure 3 • (ABOVE) Sproule WR-1200® (from Johns Manville) is a series of pre-formed, high-temperature pipe and block insulation products.
Uses and Applications
Perlite molded pipe and block insulation products combine strength at elevated temperatures, low thermal conductivity, and corrosion-resistance. They are especially useful for high temperature applications involving process piping, refractory situations, and chemical plants and refineries. They can be used for both continuous, and cyclical operations and situations that cycle in temperature, or with austenitic stainless steel piping and equipment that would otherwise be susceptible to stress corrosion cracking. The silicate binders used offer superior corrosion resistance at high temperature. Examples of applications include tanks and vessels, heat exchangers, steam piping, valve and fitting insulation, boilers, vents, and exhaust ducts. Table 1 lists the stringent requirements demanded of perlite pipe and block insulation to perform under these high temperature circumstances.
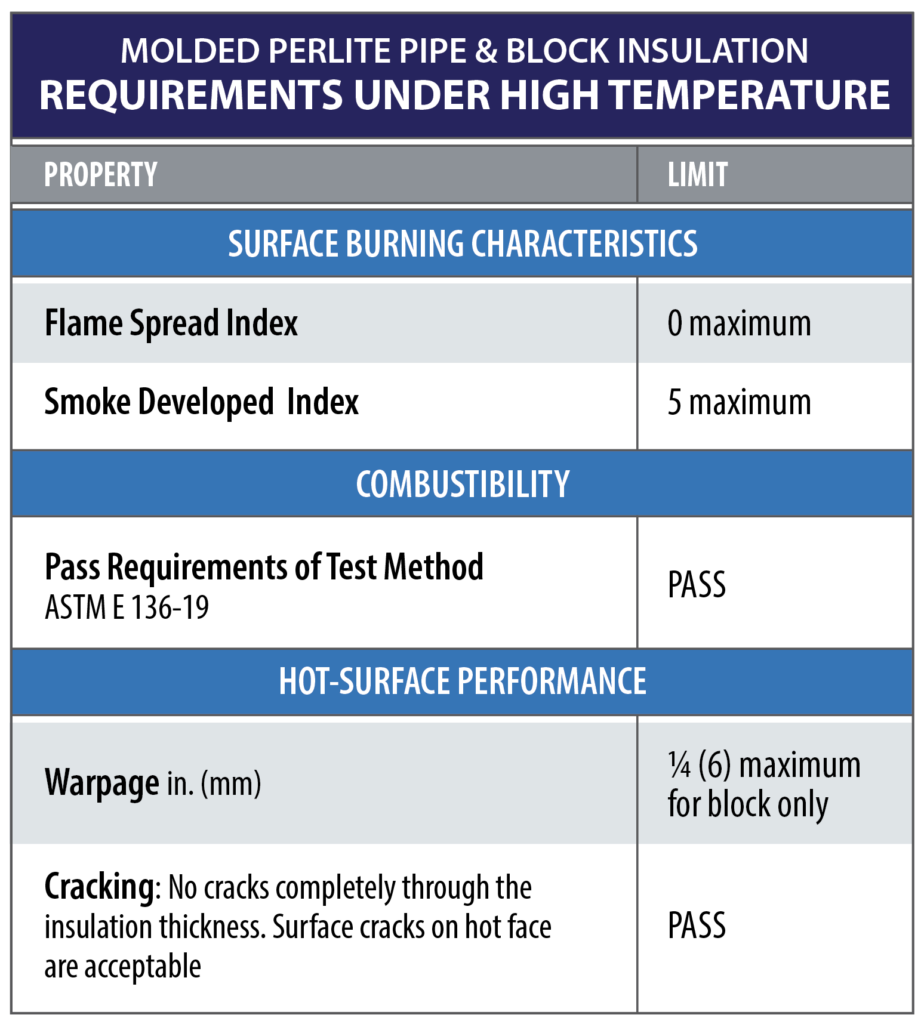
Specification of ASTM C-610 Standard
The ASTM C-610 standard covers specifications for molded perlite block, fittings and pipe thermal insulation intended for use on surfaces with temperatures between 27 and 649 °C (80-1200 °F).
BLOCKS: Block is defined in terms of lengths of either 36 or 39.4 in. (914 or 1000 mm), widths of 6 in. (152 mm), 12 in. (305 mm), 18 in. (457 mm), or 24 in. (610 mm), and in thickness from 11⁄2 to 6 in. (38 to 152 mm) in increments of 1⁄2 in. (13 mm).
PIPE: Molded expanded perlite pipe insulation is defined as hollow cylindrical shapes split in half lengthwise (in a plane including the cylindrical axis) or curved segments. The pipe insulation shall be furnished in sections or segments in lengths of either 36 or 39.4 in. (914 or 1000 mm) to fit standard sizes of pipe and tubing, and in nominal thickness from 1 to 4 in. (25 to 102 mm) in 1⁄2-in. (13-mm) increments. Inner and outer diameters shall be in accordance with those standard dimensions specified in Practice ASTM C5852.
FITTINGS: Molded expanded insulation fittings will conform to the inner and outer diameters in accordance with Practice ASTM C5852.
Product Qualification
The following are technical properties generally considered for the purposes of product characterization and qualification. Table 2 provides typical physical characteristics.
- Density
- Flexural strength
- Compressive resistance
- Surface burning characteristics
- Linear shrinkage after soaking heat
- Water absorption after heat aging
- Apparent thermal conductivity
- Hot-surface performance
- Stress corrosion cracking of austenitic stainless steel
- Weight loss by tumbling
- Mass loss corrosion rate
- Combustibility
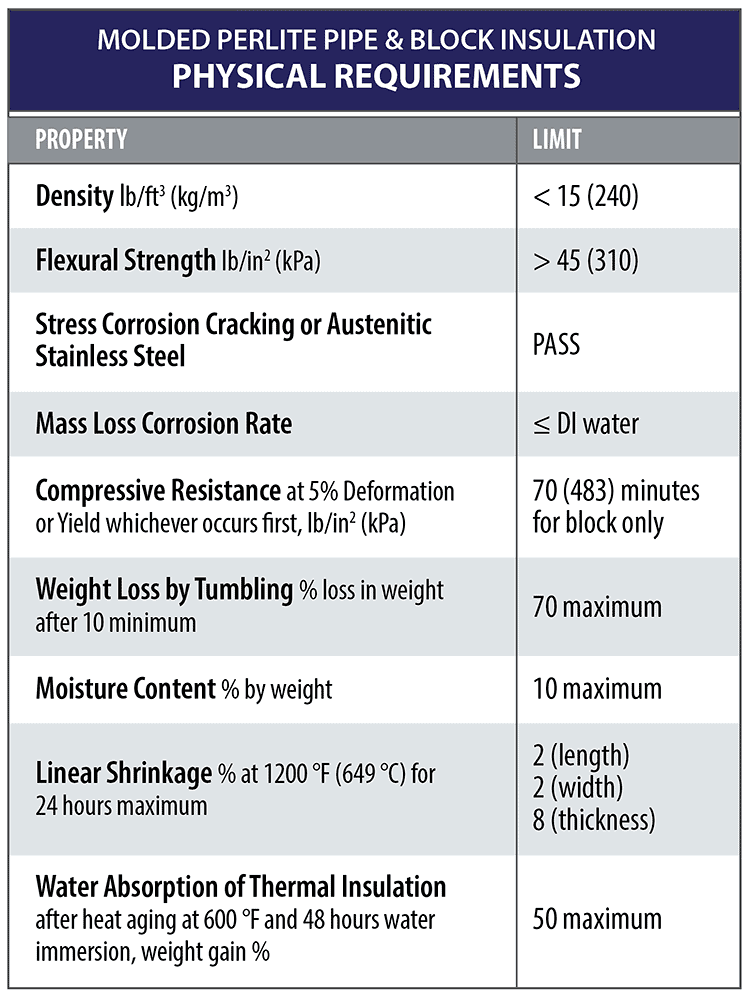
1 • ASTM Standard C610-17, 2017, ” Standard Specification for Molded Expanded Perlite Block and Pipe Thermal Insulation Specification for Concrete Aggregates,” ASTM International, West Conshohocken, PA, 2017, www.astm.org.
2 • ASTM C585-22, 2022 “Standard Practice for Inner and Outer Diameters of Thermal Insulation for Nominal Sizes of Pipe and Tubing” ASTM International, West Conshohocken, PA, 2022, www.astm.org.
To download a .pdf of the Perlite Molded Pipe and Block Insulation brochure, click here.
If you have technical questions on this topic, please email the technical contacts listed on our contact page.
Copyright © 2023 Perlite Institute All Rights Reserved