Lightweight, incombustible, and compatible with many other materials, expanded perlite others significant advantages when used in the making of masonry veneer products.
The physical characteristics of expanded perlite lend themselves to a variety of special purposes—including use as a component of lightweight manufactured stone. For a detailed explanation of perlite expansion, see info sheet: Why Perlite Works.
Expanded perlite is widely seen as an economical way to lighten concrete and plaster. But did you know it can also be used to enhance manufactured stone and masonry veneer products?
Manufactured stone (also known as simulated stone) made with perlite, is fire resistant, weighs as little as one third as much as generic versions, and
above all—is attractive!
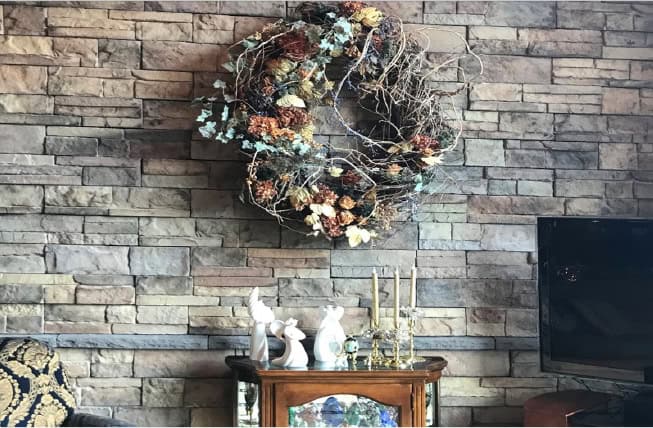
Advantages of Perlite Manufactured Stone
Perlite manufactured stone products are lightweight thereby reducing strain on workers accustomed to handling denser materials like stone. They
are less energy intensive to ship, and offer added insulating benefits resulting from the bubbles of trapped air that constitute expanded perlite.
Perlite can be used in place of materials that are denser, more costly, or harder to come by, or simply to lend alternative textural or visual appeal.
Manufactured stone products are excellent for hiding irregular wall surfaces and may be used in new construction, remodeling and in exterior applications, depending upon the binder used.
Mix Compounds
Perlite concrete and plaster aggregates conforming to ASTM specifications are commonly used in the making of manufactured stone. Binders and other components of perlite manufactured stone usually include Type I or Type III Portland cement, gypsum, lime, clay and castable or other resins. Other additions may include sand, pumice or shale, coloring agents, silicates, alkali resistant fiberglass or polypropylene shorts.
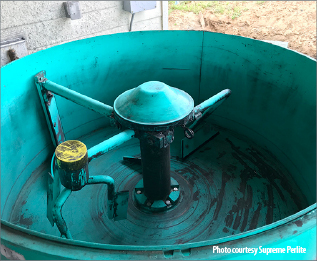
Mix designs for perlite manufactured stone products range based on application. Mixing is accomplished with ribbon, plaster or other mixers having low shear action. Paddle type and size should be chosen for the lowest shear rate.
For compressive strength data and suggestions for mix designs, see info sheet “Overview of Perlite Concrete.”
Stone Product Manufacture
Manufactured stone products may be formed by pouring or pressing the molding material into relief molds, by extruding or vibrating into wood or steel molds or forms and by die cutting. Surface finish and configuration of the stone is determined by the mold being used.
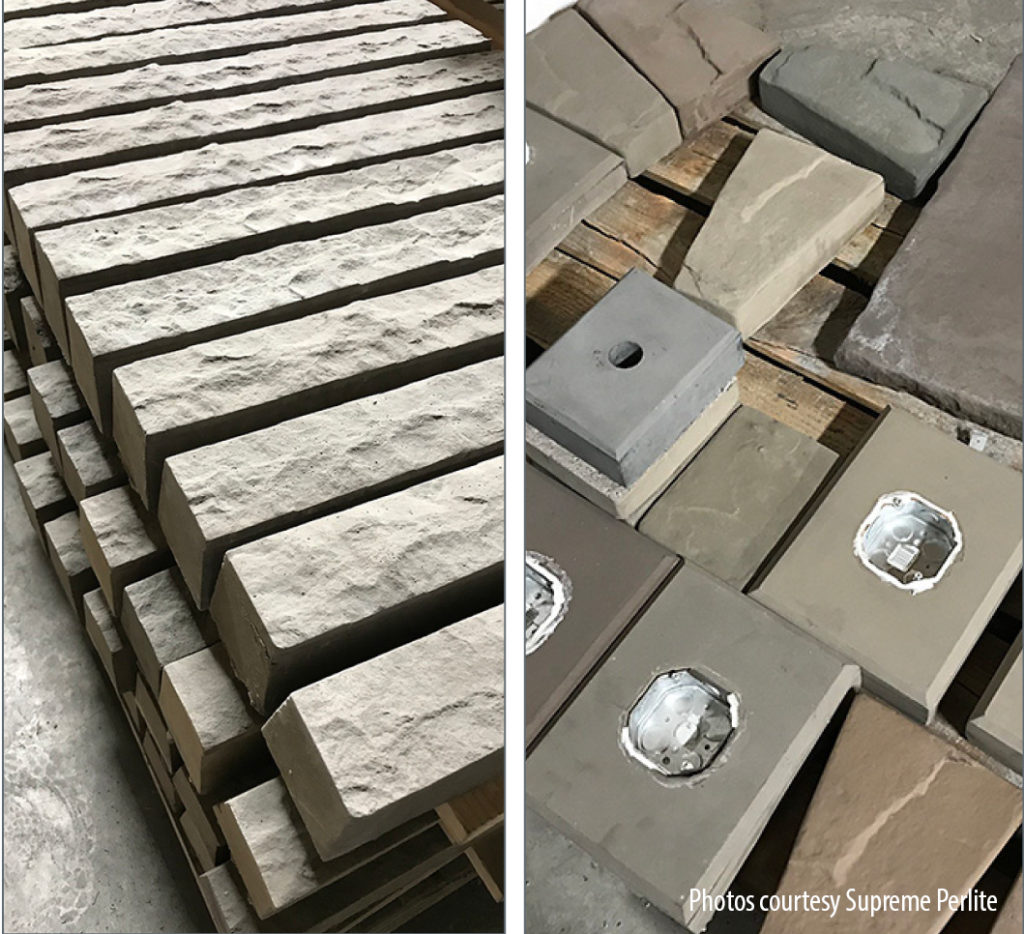
Applications for Perlite Manufactured Stone
Among the applications for lightweight perlite manufactured stone are exterior siding, fireplace logs, masonry blocks; and brick and stone for decorative exterior and interior applications.
For more information on the use of perlite in stone and masonry applications, contact your local perlite manufacturer.
To download a .pdf of the Perlite in Lightweight Manufactured Stone brochure, click here.
If you have technical questions on this topic, please email the technical contacts listed on our contact page.
Copyright © 2019 Perlite Institute All Rights Reserved