As filtration processes go, beer-making is demanding. Strict standards for clarity, flavor, purity, and bottle-to-bottle uniformity require a high-performance filter aid media.
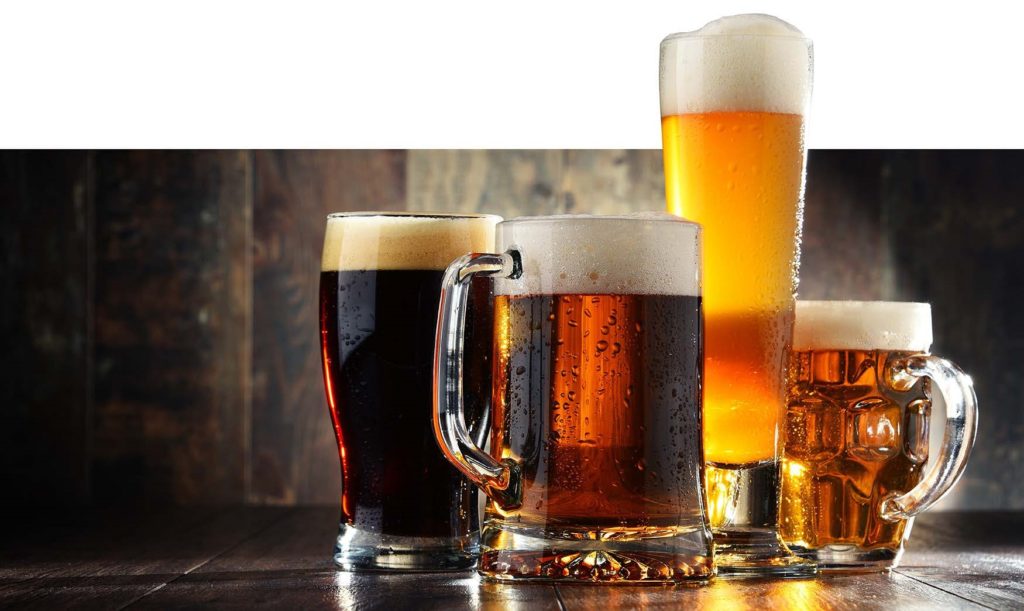
The filtration process is an important step to ensuring the quality of beer because it helps stabilize beer, and gives it a polished, clear appearance, while removing elements that might make it unpalatable. Depth filtration is widely applied for this purpose, with filter aid media playing a decisive role in processing performance and the quality of the final product.
This document presents basic aspects of beer filtration using filter aids, and the advantages of using perlite as a filter aid (PFA). PFA is superior to other alternatives due to (i) its purity and the elimination of risk from contamination by heavy metals, (ii) its low density and consequent reduction of filter aid mass, and (iii) its widespread availability and general reliability of supply.
Beer Filtration and the Significance of Filter Aids
As filtration processes go, beer-making is one of the more demanding processes because it must meet high standards for clarity, flavor, and purity, while maintaining uniform quality from bottle to bottle, and across the different brewing locations operated by the same brand. Key ingredients to maintaining that balance constitute the microbial load, the water quality, the control of yeast and bacteria content, clarification, stabilization and final filtration. The importance of filtration lies in the fact that contaminants such as particles, crystals, treatment residue, organic aggregates, bacteria and yeast can all risk affecting product quality and jeopardize the beverage’s final taste.
Filtration is the last major step in the beer-making process, and following fermentation and maturation. The aim is to remove solids—mostly yeast and other impurities—that are left in the beer following brewing. Filtration typically takes place just above 0°C in candle or plate filters until the desired clarity is achieved. More information on these and other types of filtration systems can be found in the Perlite Institute brochure Perlite Filter Aid for Vacuum & Pressure Filtration.
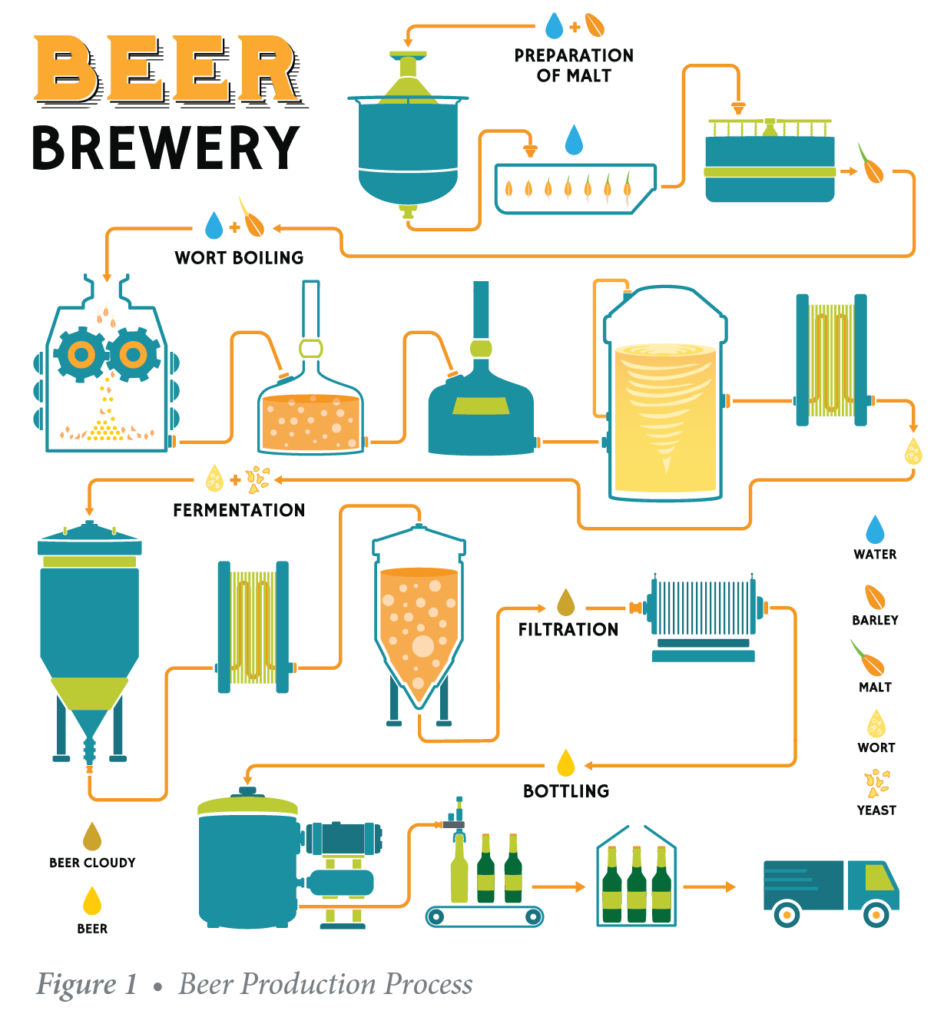
Strict standards set in the beer industry require the use of high-performance filter aid media in beer filtration. Filter aids consist of solid particles that improve filtering efficiency by building up a porous, permeable and rigid lattice structure—the filter cake—that is then used to retain solid particles and help with flow control. The septum, usually screen or cloth, serves as a support for the filter cake. The filter aid forms a porous layer on top of the septum and becomes the filtering medium that traps solids and prevents them from blinding the septum. Irregularly shaped particles interlaced and overlaying each other leave open spaces—billions of microscopic interstices—between the filter aid particles. The size of these openings is so minute that the unwanted solids are strained from the liquid, and the sheer number of openings compensates for their small size, resulting in fast flow rates and brilliant clarity.
Filter aids may be applied either as precoat on the septum and/or as body feed in the liquid (Figure 3). As precoat, filter aid forms a thin layer over the filter before the suspension is pumped to the apparatus. The precoat prevents fine particles in suspension from becoming so entangled in the filter medium that its resistance becomes excessive. Further, it facilitates the removal of cake from the septum at the end of the filtration cycle. More information on Perlite Filter Aid is available online at www.perlite.org in the Perlite Institute brochure Perlite Filter Aids Explained.
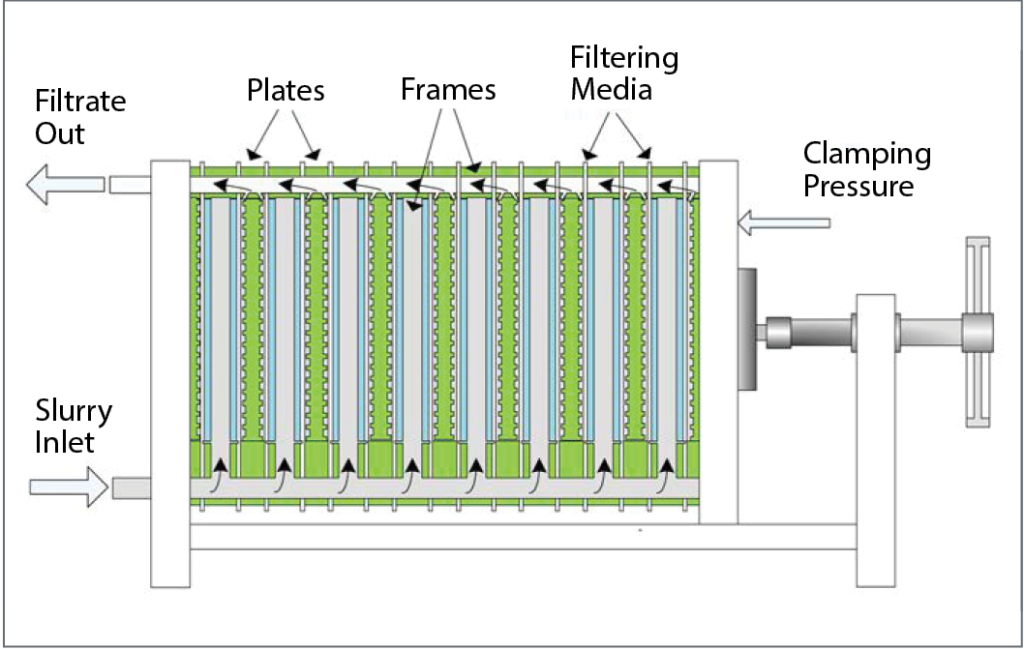
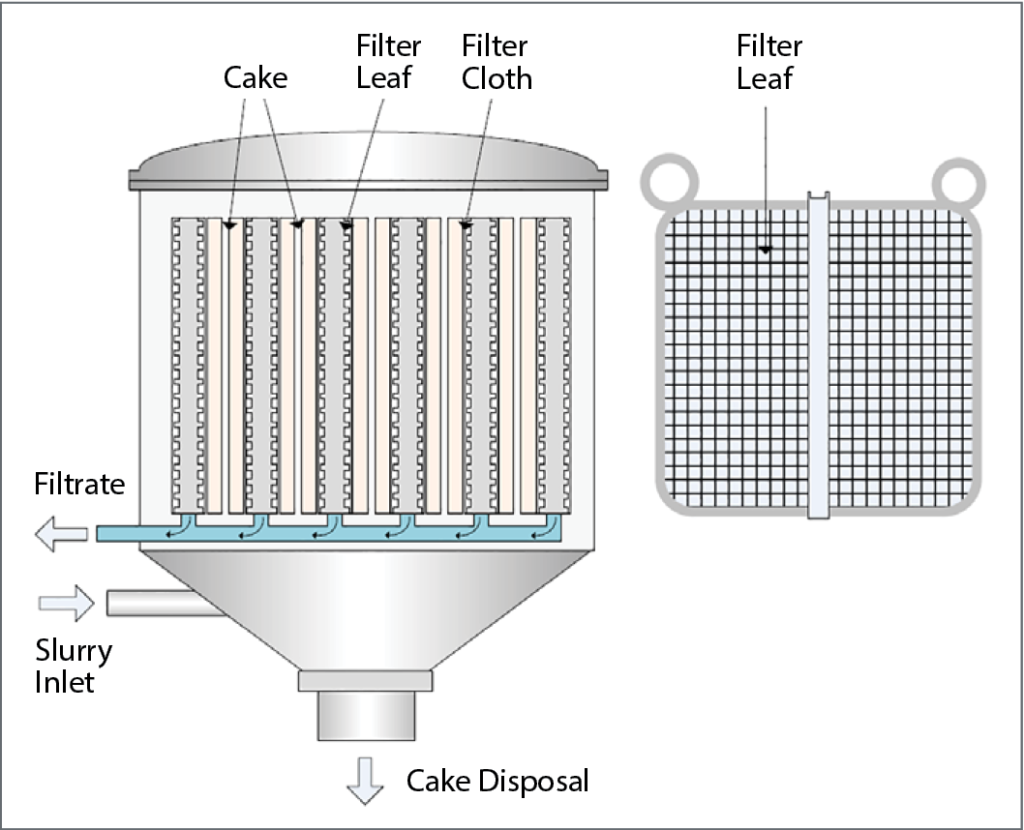
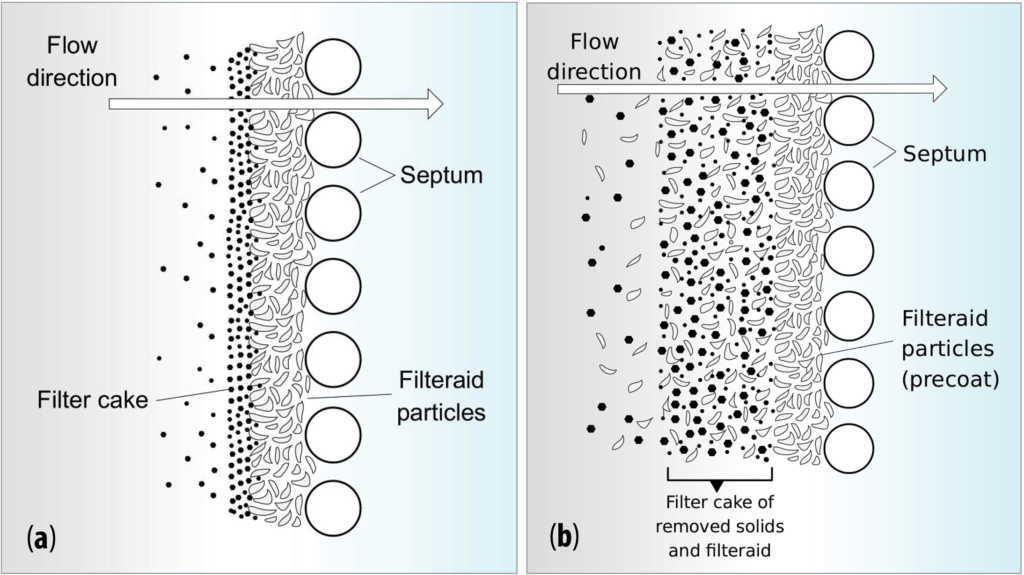
Perlite Filter Aid Properties
Perlite filter aid is created through the expansion of perlite ore, the milling of that expanded perlite, and the classification of milled expanded perlite using cyclonic air separation. Clarity is considered as the most important measure of filter aid efficiency, thus the selection of the correct grade in terms of particle size and distribution is important. Nowadays, a range of perlite filter aid grades are produced, some finer, and some coarser, with varying technical properties to optimize filtration capacity for a wide variety of applications. The various grades utilize the jagged interlocking structures of the particles to create billions of microscopic channels between the filter aid particles. When the filtration process is applied in stages, medium-sized grades are commonly at the beginning, while finer grades are used during secondary filtration.
Another important parameter for consideration is the rate of flow through the filter aid media. The flow rate is calculated using Darcy’s Law, which expresses permeability as the rate of flow of fluids through porous media. A filter medium with a permeability of 1 Darcy defines a flow of 1 cm³/s of a fluid with viscosity 1 cP (similar to water) under a pressure gradient of 1 atm/cm acting across an area of 1 cm². Experimentation is the best way to determine which filter aid grade will deliver optimum performance and effectiveness.
Due to its structure and physicochemical properties, perlite filter aid is currently used in a wide range of filtration processes within the food industry. It is the choice of many producers for the following reasons:
- It offers consistent, reproducible, and highly effective results.
- It is available in a wide range of grades and sizes befitting various permeability levels.
- It is chemically inert, non-toxic, odorless, and environmentally safe.
- It is sterile, having been heated to temperatures over 900°C.
- It meets the requirements of the US Food Chemical Codex (FCC) and relevant EU regulations.
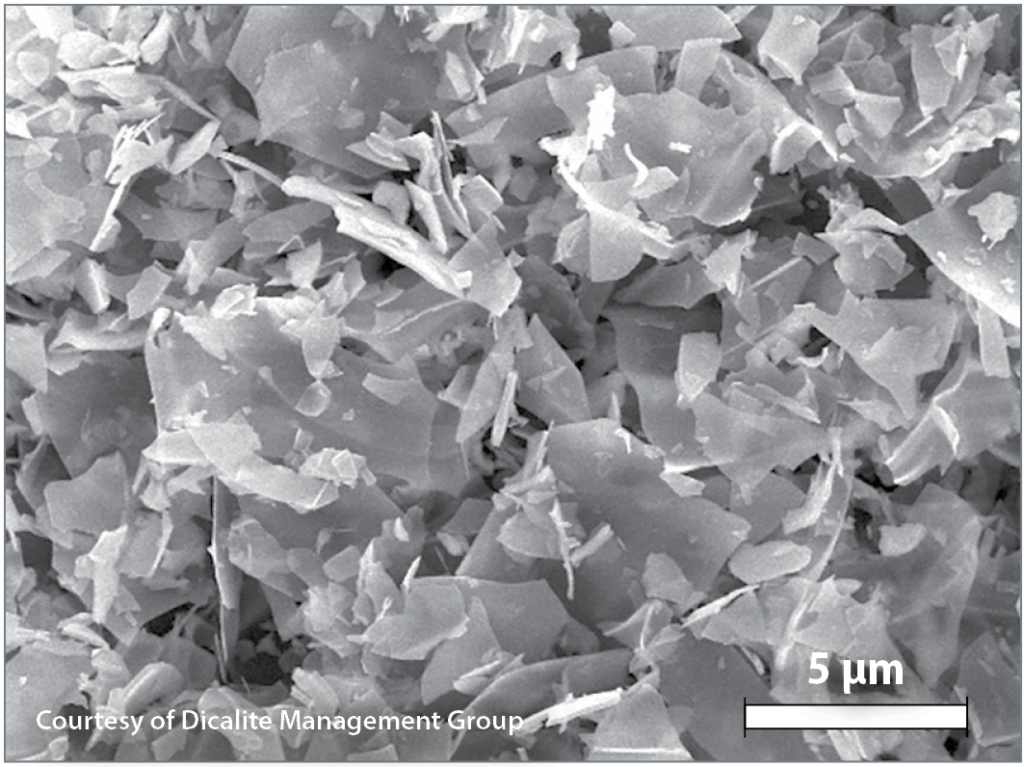
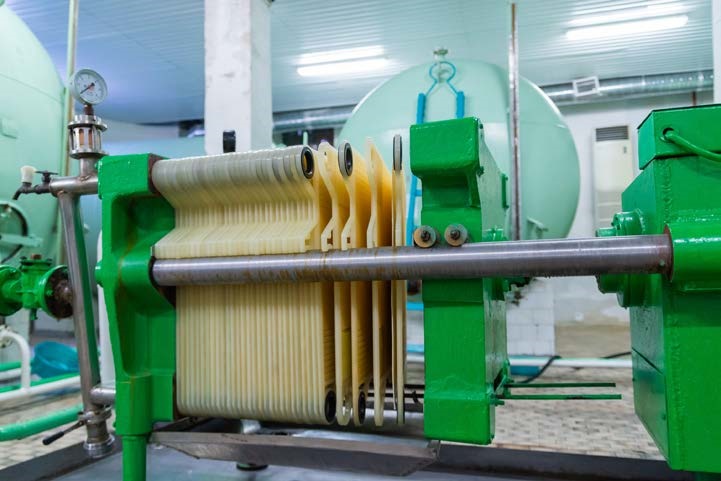
Advantages of Perlite Filter Aid Over Diatomaceous Earth
Perlite possesses characteristics that are more advantageous than Diatomaceous Earth (DE), in terms of health and safety, availability and performance:
- DE can contain arsenic and other heavy metals that can be transferred to beer during processing.1–3
- DE possess soluble iron that can affect the quality of edible and drinkable products.4
- The level of respirable crystalline silica is also a primary concern for manufacturers and their employees. PFA contains little to no respirable crystalline silica, making it ultimately a healthier and safer product to handle.5, 6
- Contrary to DE, perlite filter aid is not subject to the strict regulations governing its disposal.4
- On a physical note, perlite has 30-50% less bulk density compared with DE. On a volume to volume basis, the amount of perlite required typically requires 30-50% less mass than is required when using DE.7, 8
- A wide network of suppliers ensures quick and uninterrupted local supply. By contrast, DE can have significantly longer lead times and require that larger quantities are kept on-hand to guard against interruptions in supply.
Easy Disposal and Reuse Options
Perlite filter aid is not a hazardous substance and is Generally Regarded as Safe (GRAS) for use with humans and animals. It is also chemically inert and odorless, therefore, disposal of spent perlite filter aids is not subject to special regulations. Often, spent filter cake may be down-cycled for further use, resulting in the elimination of waste through reuse of the entire filtrate. More information on this can be found in the document Perlite Filter Aid and the Circular Economy available on the Perlite Institute website, at www.perlite.org. Some typical reuse applications include:†
- As animal feed supplement
- As compost and soil amendment for crop production
- Production of tartaric acid
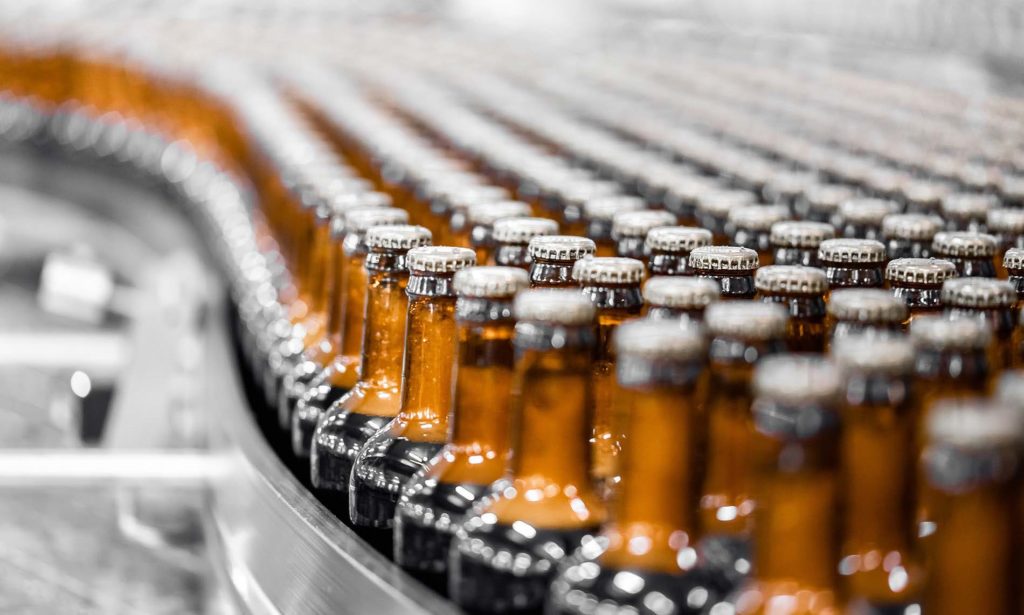
Beer and Soluble Iron
Iron occurs naturally in beer as salts or ions (incl. Fe2+ and Fe3+ cations). Iron is commonly found in trace amounts below 0.1 mg/L, but in concentrations over 1 mg/L, tannins may bond with iron ions, adding to a metallic or unpleasant aftertaste and/or brown tinge to the beer. Even these low levels of iron can be detrimental to the stability of beer because they increase the likelihood of reactive oxygen species being produced. The presence of such species speeds the rate of beer staling and the oxidation of polyphenols that leads to haze. The only benefit from iron presence is that it enhances gushing; in small-scale trials it has been detected that Fe3+ causes gushing, whereas Fe2+ did not have any effect.10
The major sources of soluble iron in beer are the brewing water itself and the filter aid media. Special treatment of the brewing water, called deferrization, is carried out if the iron concentration is above 0.12 mg/L. As for the filter aid media, it is generally recommended to start with a filter aid having minimal iron content in the first place. The average concentration of dissolved iron in beer resulting from perlite filter aid is below 15 ppm (mg/kg), while some sources result in even lower levels – less than 1.0 ppm. The simplest, most accurate way of determining the level of iron and other trace elements in beer (e.g. Na, K, Ca, Mg, Pb, Ni, Cu and Zn)11–13 is with atomic absorption spectroscopy.
†“Perlite Filter Aid and the Circular Economy”, the Perlite Institute webpage, https://www.perlite.org/wp-content/uploads/2021/12/PerliteFilterAids-CircularEconomy.pdf
BIBLIOGRAPHY
[1] Redan BW, Jablonski JE, Halverson C, Jaganathan J, Mabud MA, Jackson LS. Factors Affecting Transfer of the Heavy Metals Arsenic, Lead, and Cadmium from Diatomaceous-Earth Filter Aids to Alcoholic Beverages during Laboratory-Scale Filtration. J Agric Food Chem. 2019;67(9):2670-2678. doi:10.1021/acs.jafc.8b06062[2] Coelhan M. Release of arsenic from kieselguhr used as filtration aid in the food industry. In: 5th International Congress on Arsenic in the Environment. Buenos Aires; 2014.
[3] Passaghe P, Bertoli S, Tubaro F, Buiatti S. Monitoring of some selected heavy metals throughout the brewing process of craft beers by inductively coupled plasma mass spectrometry. Eur Food Res Technol. 2015;241(2):199-215. doi:10.1007/s00217-015-2445-7
[4] Jackson RS. Post-Fermentation Treatments and Related Topics.; 2014.
doi:10.1016/b978-0-12-381468-5.00008-7
[5] Nattrass C, Horwell CJ, Damby DE, Kermanizadeh A, Brown DM, Stone V. The global variability of diatomaceous earth toxicity: A physicochemical and in vitro investigation. J Occup Med Toxicol. 2015;10(1):1-16. doi:10.1186/s12995-015- 0064-7
[6] Park R, Rice F, Stayner L, Smith R, Gilbert S, Checkoway H. Exposure to crystalline silica, silicosis, and lung disease other than cancer in diatomaceous earth industry workers: A quantitative risk assessment. Occup Environ Med. 2002;59(1):36-43. doi:10.1136/oem.59.1.36
[7] Cheremisinoff NP. Filter Media and Use of Filter Aids. Liq Filtr. 1998:19-58. doi:10.1016/b978-075067047-0/50003-9
[8] Perlmutter BA. Chapter 1 – Introduction. Solid-Liquid Filtr. 2015:1-20.
doi:10.1016/B978-0-12-803053-0.00001-8
[9] Jakob O. The Oxford Companion to Beer definition of iron. https://beerandbrewing.com/dictionary/z0QfFWKntf/. Published 2022.
[10] Anger H-MSSDH and KP. Handbook of Brewing Processes Technology Markets-Wiley.; 2006
[11] Perkin E. Analytical Methods for Atomic Absorption Spectroscopy. Analytical Methods. 1996:216.
[12] Tenney RI, Duensing WJ. Determination of Soluble Iron in Filter Aids. J Am Soc Brew Chem. 1976;34(2):120-122. doi:10.1080/03610470.1976.12006208
[13] Olalla M, González MC, Cabrera C, López MC. Optimized Determination of Iron in Grape Juice, Wines, and Other Alcoholic Beverages by Atomic Absorption Spectrometry. J AOAC Int. 2000;83(1):189-195. doi:10.1093/jaoac/83.1.189
To download a .pdf of the Beer Filtration brochure, click here.
If you have technical questions on this topic, please email the technical contacts listed on our contact page.
Copyright © 2022 Perlite Institute All Rights Reserved