Perlite concrete pipe insulation provides a seamless, lightweight, quality thermal insulation that is also fire, rot, and vermin proof.
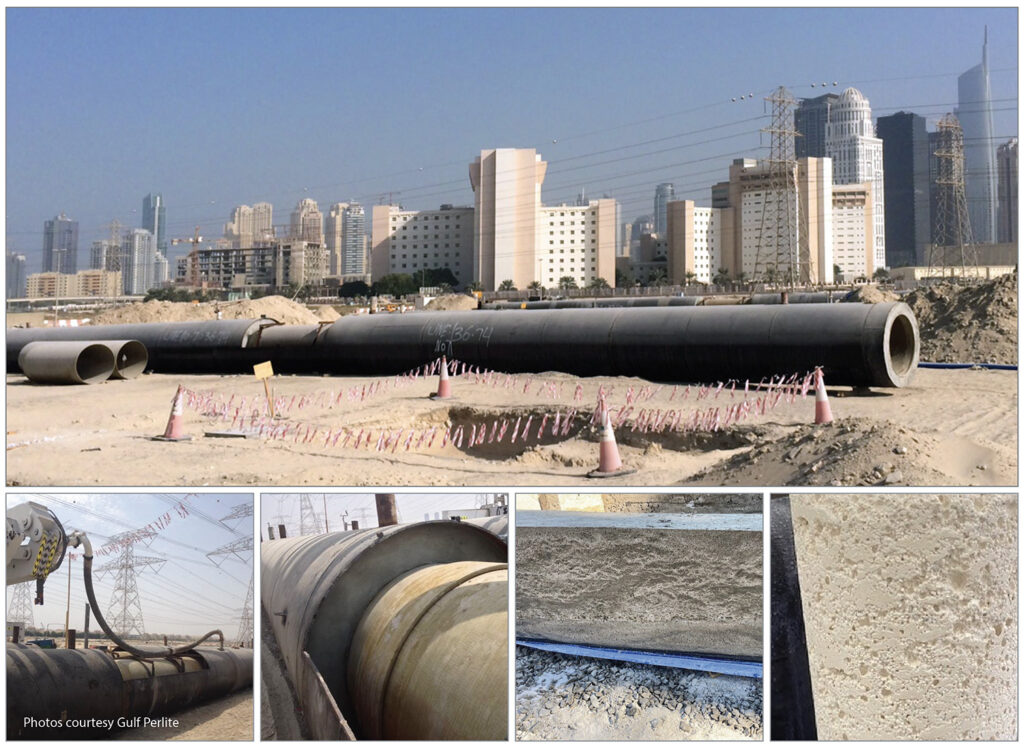
Above from Left • Pumping perlite concrete into form around pipe section; cured insulative sleeve around pipe; perlite concrete blocks placed to support insulated pipe; perlite concrete test cylinder.
Lightweight perlite insulating concrete can play multiple roles in underground pipe and duct installations. In addition to providing quality thermal insulation, perlite concrete insulation can also serve as a supporting envelope. This latter advantage is of special importance when pipe or ducts are laid under roadways, parking lots or other areas subject to traffic. Perlite concrete pipe insulation provides a monolithic (seamless) insulation for the length of a pipe or duct. Additionally, perlite insulating concrete is permanent, fire proof, rot proof and vermin proof.
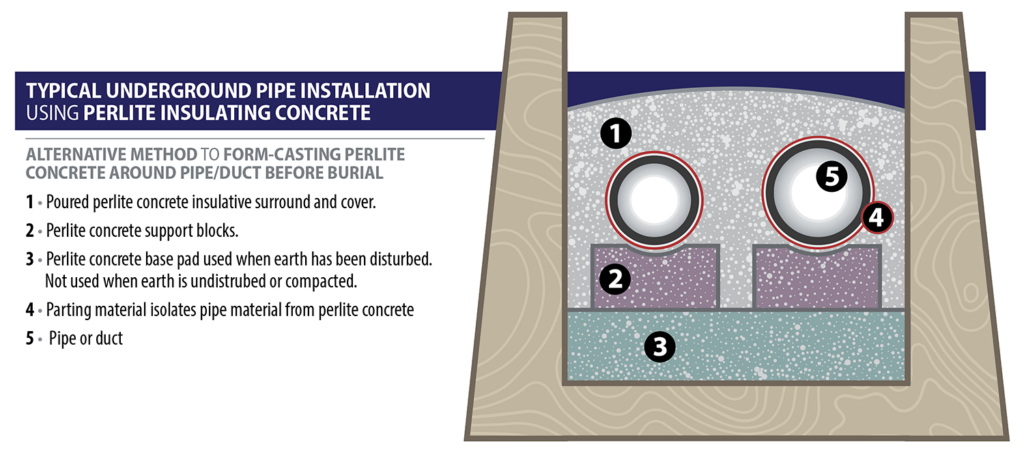
Stable or Compacted Soils
Where there is stable or compacted soil, pipe or ducting may be supported on precast perlite concrete support blocks in the bottom of a trench and a perlite concrete cover poured into the trench area. Depth of concrete cover and pipe spacing will depend on the size of pipe or duct to be insulated as well as operating temperatures. The perlite cover should be waterproofed by encasing the perlite concrete with a polyvinyl chloride (PVC) membrane. Internal vent drain lines may be required. If operating temperatures are in excess of 800°F (427°C) Aluminite cement should be employed. Prior to pouring concrete, pipe and ducts should be wrapped with a parting material such as wax coated corrugated paper to prevent the perlite concrete from adhering to the pipe and to permit free longitudinal movement of the pipe as a result of temperature changes.
Disturbed or Loose Soils
When disturbed soils are encountered in the trench area, a perlite concrete base pad should be poured first. Precast perlite concrete support blocks are then placed on top of the base pad and the installation proceeds as for installations in compacted soils.
Expansion Loops or Ells
Expansion loops and ells must be carefully designed as there will be pipe or duct movement in the perlite concrete insulation as a result of temperature changes. Depending on the design, metal pan blockouts can be used to isolate the pipe or ducts from the insulation in those areas where there is excessive movement. Double wraps of 1-1/2 inch (4 cm) foil faced fiberglass may also be used to accommodate pipe movement at elbows, expansion loops, expansion Zs and U-bends.
Heavy Traffic Areas
Where there is heavy traffic loading on the soil above an insulated pipe as when running pipe under parking lots or highways, the designer should take this loading into account.
To download a .pdf of the Insulating Underground Pipe and Ducting With Perlite Insulating Concrete brochure, click here.
If you have technical questions on this topic, please email the technical contacts listed on our contact page.
Copyright © 2023 Perlite Institute All Rights Reserved